Auto Workers Direct Momentum Toward Organizing Plants Across the U.S.
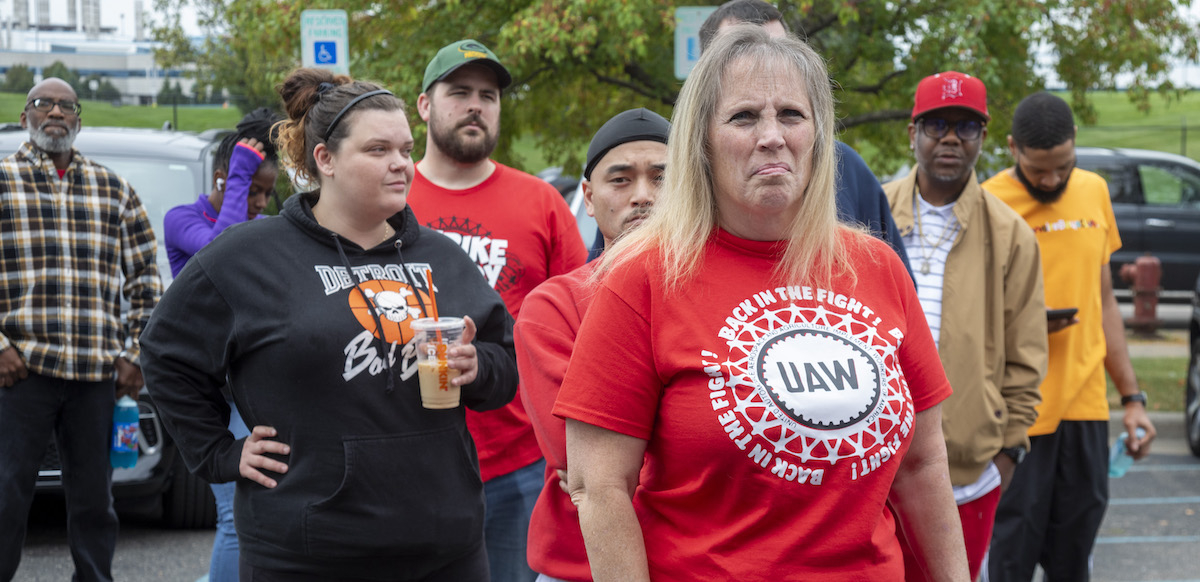
Auto workers in Detroit wait to enter a meeting on September 10 about their impending Big 3 strike. The union’s gains at the Big 3 have drawn the attention of non-union auto workers. Photo: Jim West, jimwestphoto.com.
“The company knows that Toyota workers are watching,” said Auto Workers President Shawn Fain on November 3. “And when the time comes, Toyota workers and all non-union auto workers are going to be ready to stand up.”
That time has come—yesterday the UAW announced its plan, already in motion, to organize the whole auto sector. “Workers across the country, from the West to the Midwest and especially in the South, are reaching out to join our movement and to join the UAW,” said Fain in a new video.
The union says thousands of workers have reached out asking for support in unionizing their auto plants. They’ve scoured the old websites from previous union drives and filled out forms to be put in touch with an organizer.
“To all the auto workers out there working without the benefits of a union: Now it’s your turn,” he said, inviting auto workers to join the organizing push and telling them where they can electronically sign union cards, at UAW.org/join.
Thousands of non-union auto workers are already organizing across the 10 foreign-owned transplants, including Toyota, Hyundai, and Mercedes, as well as in the electric vehicle sector at Tesla, Rivian, and Lucid. Overall, the organizing drive will cover 150,000 workers—roughly the same number of workers covered under the Big 3 contracts—across 13 automakers.
At Rivian’s electric vehicle plant in Bloomington, Illinois, workers have already built an organizing committee, surveyed 1,000 of their co-workers on major job improvements, and run petitions demanding longer breaks. There are about 5,000 hourly workers at the plant.
“Rivian already knows that we are organizing,” said Sonia Williams, who asked to use a pseudonym for fear the company would retaliate. “We’re not shy about it. We have given them opportunities to meet with us. They called in sick both times. We’ve also handed them petitions.”
UAW membership has dwindled from 1.5 million in 1979 to 383,000 in 2023. Fresh off reversing decades of concessions in auto, the union’s reform leadership is now also seeking to reverse its membership decline.
The UAW is hoping to springboard from union reform and a lucrative contract deal into new organizing, betting that workers will want to join a transformed, fighting union.
STAND-UP 2.0
In the video, Fain pointed to the strategy of the Big 3 auto workers’ Stand-Up Strike, which involved a calibrated ramp-up of work stoppages until the automakers—Ford, Stellantis, and General Motors— caved to worker demands. The strategy kept the companies guessing throughout.
Now, the UAW is deploying a similar strategy, hoping to catch the companies off guard as to where a union campaign may pop up. The union is encouraging workers to run campaigns simultaneously across the non-union automakers.
Under the plan, once 30 percent of workers at any given plant have signed union cards, workers will go public with their drive. Some plants have already met that threshold, according to the UAW. At the 50 percent mark, workers rally their co-workers, families, neighbors, and community leaders, according to the union.
As soon as 70 percent of workers at a given plant sign cards, and have a committee made up of workers from every shift and job classification, they will demand voluntary recognition of their union. If the company refuses, the workers file for an election with the National Labor Relations Board.
The UAW is breaking away from previous years-long efforts at single plants in favor of what it calls a momentum organizing approach, coupled with a strong inside organizing campaign.
That approach to taking on the whole auto sector is predicated on generating momentum from each fight, opening multiple fronts in what the union hopes will swell into a tidal wave of organizing. UAW is drawing inspiration from the ongoing organizing push by Starbucks workers.
“The Starbucks Workers United campaign showed that it is possible to organize hundreds of workplaces, even at the most anti-union billion-dollar corporations,” said John Logan, a professor of labor studies at San Francisco State University. SBWU has organized 360 stores in two years. “Building on the momentum of its historic contract at the Big 3, there's no reason why the UAW cannot organize at multiple non-union plants in the South. The question is whether, like the Starbucks campaign, it’s able to capture the imagination of the workers.”
In a press release, the UAW singled out Toyota’s Georgetown, Kentucky, assembly complex where 7,800 workers build the company’s Camry, the Rav 4 sport utility vehicle, and the luxury Lexus ES.
THE UAW BUMP
As soon as the union announced the big wage and benefit gains that Big 3 workers had won, Toyota, Honda, and Hyundai rushed to boost pay. Honda announced wage hikes of 11 percent; Hyundai bumped pay by 25 percent over the next four years. Toyota has offered its workers a smaller 9 percent raise to dissuade them from organizing a union.
Meanwhile Toyota has hauled in a quarter-trillion in profit in the past decade, according to the union. The company’s profits have surged 30 percent, while its CEO’s pay has increased by 125 percent.
“Toyota isn't giving out raises out of the goodness of their heart,” Fain said in a video statement shared by More Perfect Union. “Toyota is the largest and most profitable auto company in the world. They could have just as easily raised wages a month ago or a year ago. They did it now because the company knows we're coming for them.
“Even though you're not yet members of our union, that pay raise Toyota's giving you is the UAW bump,” Fain said, addressing Toyota workers. “UAW. That stands for ‘You are welcome.’
“You are welcome to join our Stand-Up movement. If this is what Toyota gives you when the Big 3 stand up and fight, imagine what you could accomplish if you join the UAW and stand up and fight for yourselves.”
HIGH PRODUCTIVITY, LONG HOURS
The pay raise hasn’t changed Toyota worker Jeff Allen’s resolve to organize with his co-workers at Georgetown. “We are tired of going backwards while our company continues to move forward,” said Allen. “We want the security of having a contract to protect our total compensation for now and our future.”
At Hyundai in Montgomery, Alabama, 12-year team member Gilbert Brooks has had organizing a union on his mind since he was hired. He had been a member of the Steelworkers for 11 years at the Goodyear tire factory in Anniston. At Hyundai, 3,500 hourly, temporary, and contract employees assemble the Santa Fe, Tucson, and Santa Cruz, the Genesis GV70, and the Electrified GV70.
“We build 1,500 cars a day and 500 cars a shift,” said Brooks. When measured by the speed a car is produced, this is the second-most-productive plant in the world. That high productivity, he says, should be rewarded with higher wages. He earns $28.35 an hour, which will go up to around $30 in January after the promised wage hike. The company is also offering a $4,000 bonus. New hires start at around $19.
Over the past three years, Hyundai’s profits have soared 75 percent, while its vehicle prices rose 32 percent. “We are underpaid and overworked,” Brooks said. His point of comparison is what his ex-wife will earn at GM’s Spring Hill plant in Tennessee: she’ll go from $25 to $35 an hour right away under the new UAW contract at GM.
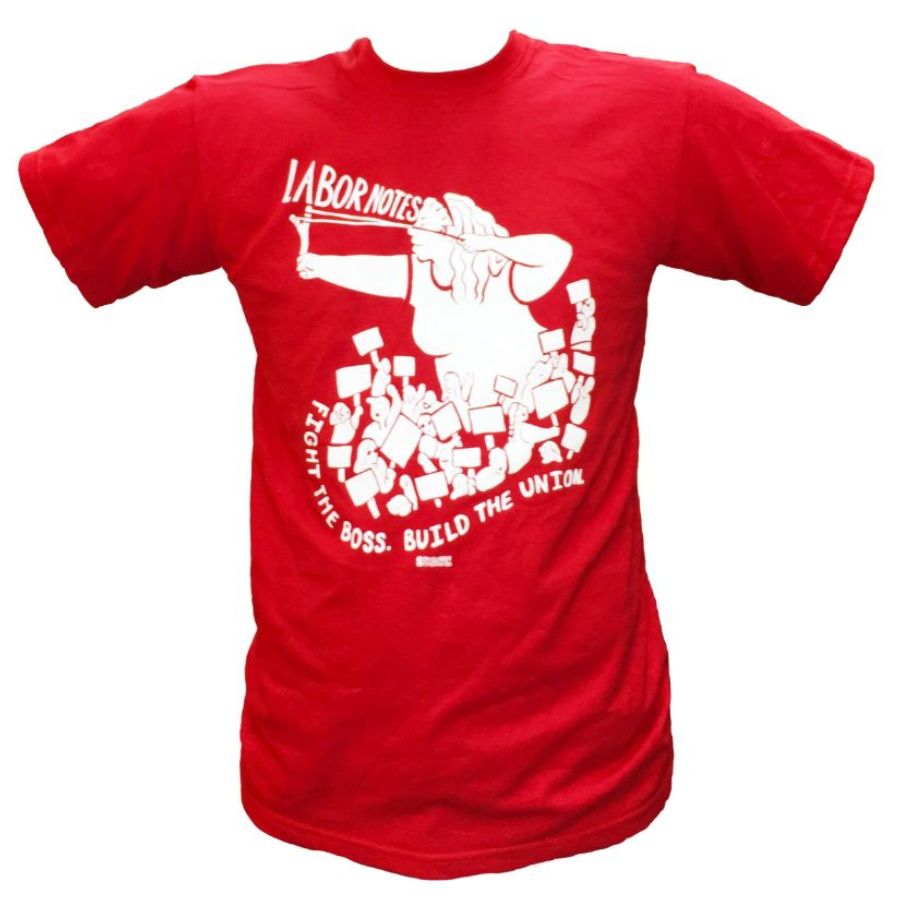
SUPPORT LABOR NOTES
BECOME A MONTHLY DONOR
Give $10 a month or more and get our "Fight the Boss, Build the Union" T-shirt.
But the main sticking points are safety and respect on the job. He said the company forces workers to do jobs that really require two people and changes work rules on a whim. The result is injuries.
Since 2012, Brooks said, he has undergone two neck and two rotator cuff surgeries. He sustained the first work-related injuries in 2014 after grueling 10-hour shifts on the trim line installing brackets on vehicles. The job required him to lift his arms over his head all day to screw the brackets on.
When he complained to management about the pain, Brooks said, the in-house clinic gave him heat packs or ice packs (a common practice also in meatpacking) to evade mandatory reporting of injuries to the Occupational Safety and Health Administration. He had to seek medical care from an outside provider.
CARROTS AND STICKS
At the time, in 2014, the company didn’t even offer light duty for injured workers—but once word spread around the plant that a unionization campaign was afoot, Brooks said, Hyundai used a mix of carrots and sticks to beat back the union drive, including offering light duty and bonuses. Brooks said the campaign never got enough signed authorization cards to file for a union election. He blames the demoralization that swept the plant in the wake of the UAW’s defeated drive at Volkswagen in Chattanooga that year, combined with the company’s threat to close down and relocate. Chattanooga VW workers tried and lost again in 2019.
But momentum is now on the organizing committee's side at Hyundai, as more people have come out in support of the union after the Big 3 contract fight, Brooks said. “Everything needs to change, from the safety inside the plant to the treatment of the people that are doing the work that makes the company run.”
At Rivian, Williams said workers’ main workplace concerns revolve around safety and time off. Injuries include a crushed hand, a broken foot, a sliced ear, and broken ribs, according to complaints filed with OSHA. Workers attribute these injuries to the breakneck pace of production. There’s worse to come. Just this month, the company raised its production forecasts for the full year by 2,000 vehicles, to 54,000 units.
In 2022, workers often put in 12-hour days, seven days a week. But Williams said the company changed its scheduling to 12-hour shifts, four days a week, in anticipation of Illinois’s One Day Rest in Seven Act, where an employee is entitled to at least one day off in any consecutive seven-day period. The law went into effect in January 2023.
Rivian has found other ways to monopolize workers’ time, including reducing their sick hours from 80 to 40 per year in January 2023. Meanwhile, salaried employees have unlimited paid vacations, according to a screenshot shared with Labor Notes. Workers have also filed complaints with OSHA over a lack of fire exits.
THE ALABAMA DISCOUNT
A challenge for the union is that auto manufacturing jobs pay well above other options in the low-wage states of the South. There’s also less familiarity with unions, especially among younger workers. The unionization rate in Alabama, for example, is 7.2 percent. When the transplants located their manufacturing in the South, this factored into their calculation.
“It’s the Alabama discount,” said Jeremy Kimbrell, who earns $32 an hour after 24 years on the job at Mercedes-Benz. The German-based automaker manufactures its highly profitable luxury SUVs and Maybach GLS in Tuscaloosa County, Alabama, and built an electric battery plant last year in nearby Woodstock. The mammoth Mercedes plant, covered in gleaming metallic panels, was built in a pine forest in 1997.
At the time of its initial investment, Alabama forked over $300 million in tax breaks and other subsidies to attract Mercedes-Benz to the state, claiming that the company would create 1,500 jobs and another 15,000 to 17,000 related jobs.“That amounts to $200,000 for each job—18 times what Tennessee paid for a Nissan plant in 1980, more than 7 times what Tennessee paid for the General Motors Saturn plant in 1985, 4 times what Kentucky paid for a Toyota plant in 1985 and 3 times what South Carolina paid for a BMW plant in 1992,” according to a New York Times analysis from 1996.
Since then, the company has expanded its operations in the state. It employs 6,300 workers at two large body shops that feed into one paint shop, two assembly shops, and a logistics center, as well as a global service parts distribution center, a consolidation center, and the new EV battery plant.
Kimbrell has been part of two foiled efforts to organize the plant. “In the past when we ran campaigns, I would tell people, we have to make a marginal argument that the Big 3 are getting a little more money, they got pensions, and a little more benefits,” he said.
“When you put it on paper, it was a marginal argument and a lot of people would say, ‘Well, we're down here in Alabama. We’re right-to-work and that’s just to be expected.’ Now the difference has got so much greater since the Big 3 has increased its formula on profit-sharing, and got some really nice raises.”
Kimbrell and his co-workers compare that to the 87-cent raise they got in October, which he called “a slap in the face.”
“As far as we beg for raises, we're not sitting down as equals at the negotiating table,” he said.
With the UAW’s contract settlement in the news, Kimbrell said, his co-workers are beginning to come around to the benefit and power of a union. “They understand that the employer just doesn't respect us as workers,” he said. “They're giving what they think they can get by with; they’re not giving us our equal share.”
Before the 2008 recession, workers earned overtime after eight hours in a day. Now it kicks in after 40 hours in a week.
They also used to get a $500 bonus on the Fourth of July. In the early 2000s, Mercedes-Benz launched what it calls “team share,” which workers find opaque—its bonuses aren’t pegged to company profits as in a profit-sharing formula. The company introduced a two-tier system, where workers doing the same job earn different pay and benefits starting in January 2020.
The recently ratified Big 3 agreements eliminate wage tiers almost entirely.
‘YOU CAN BUILD SOMETHING POWERFUL’
Favoritism and disrespect also rankle workers at the Mercedes plant. And benefits and conditions have deteriorated. Workers are on what is called a six-by-ten schedule—they work 10-hour shifts, six days in a row, on a three-team rotation.
“Most places where I've ever organized, even when the issue is pay, what really motivates workers is respect and dignity,” said Gene Bruskin, who led a successful union campaign at a Smithfield pork processing plant in North Carolina in 2008. “If they feel disrespected, and there's no dignity on the job, people are unhappy. If you can tap into that deep-seated disrespect, allow that to sort of come out, then you can build something powerful.”
Williams said Rivian turned her into one of the key organizers of the union drive after watching management promote a team leader who she and her co-workers had reported for harassment. “Instead of firing him, they promoted him to a manager and got him to a different shift, so that he was away from us troublemakers,” she said. “I got marked as pro-union.”
Management began grilling her about her alleged union leadership role, peppering her with questions about the union drive and worker activities. “And the funny thing was at that time period, I was union-neutral," she said. "I figured if they're already gonna punish me for it, I might as well just go ahead and do it.”