Workers' Just-in-Time Moment
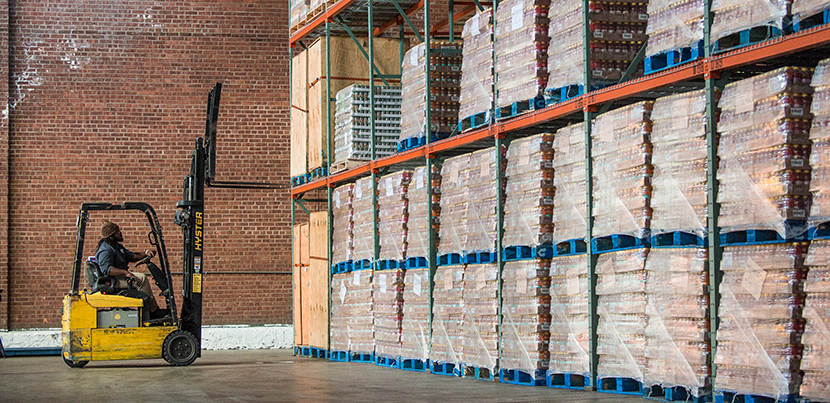
Contrary to much pundit commentary, technology does not replace the human links in the supply chain. Photo: United States Department of Agriculture.
From the Black Plague of the Middle Ages to the flu pandemic of 1918 to COVID-19, disease and pestilence have always followed two of humanity’s most well-trod paths: those of war and trade.
When the plague ravaged Europe in the 14th century it took years to cross the Silk Road from Asia to Europe and then to cover that continent through the footsteps of traders and the mobile armies of the Hundred Years War. The influenza of 1918 followed the trenches and troop movements of World War I in months.
When the coronavirus hit Wuhan, it took just days to spread across China and only a couple of weeks to follow the supply chains and trade routes of today’s just-in-time capitalism—the warehouses, rail depots, intermodal yards, airports, sea ports, and all the interpersonal contact at the connecting points—to the Middle East, then Europe, then North America. By the beginning of March it had reached 72 countries.
Three decades of streamlining and refining the movement of goods along tech-enhanced but labor-intensive supply chains have accelerated the speed of disease transmission as well as of commodities and money. But the very speed of these taut arteries of commerce has also increased their vulnerability to disruption.
VULNERABLE SUPPLY CHAINS
The hands of labor that make, move, and deliver our essential goods and services can also stop them. The billions of dollars of sunk infrastructure, the just-in-time race to the next customer in the chain, and the competition that drives the firms along these conduits of value make them vulnerable to disruption.
Supply chains, however, are complex and often changing. It takes strategic thinking and solidarity across company, industry, occupational, geographic, gender, and racial lines to take full advantage of the “ripple effect” a well-placed action can have on employers.
Think of key warehouses and distribution centers, of the fixed routes of road and rail traffic, of the impact on companies up and down the supply chain. But most of all think about the huge concentrations of 4 million or so logistics workers in the major U.S. metro areas that are the hubs of all this economic movement.
The pandemic has graphically demonstrated the centrality of the “human networks” that keep the global supply chains moving. That is, all those who produce the goods and those that bring them to the factory, the hospital, the supermarket, or your self-isolating home.
Contrary to much pundit commentary, technology does not replace the human links in the chain. As the New York Times reported April 5, “For all of its high-tech sophistication, Amazon’s vast e-commerce business is dependent on an army of workers operating in warehouses they now fear are contaminated with the coronavirus.” “None of this works without our employees,” a top Amazon executive admitted.
LEVERAGE AS COMPANIES STREAMLINE
Workers have leverage particularly when companies seek to streamline or alter their supply chains. And streamline they will. The recession that began just before the coronavirus took hold will deepen further despite all the government spending. With the recession will come a shake-up and concentration of firms of all kinds, via mergers, closings, and consolidations. These will in turn affect their supply chains.
A study by the World Economic Forum (aka, the Davos billionaires club), done a year before the virus spread, was already predicting a shake-up of corporate organization. A continued recession makes this almost inevitable as companies go under, merge, and fight to hang on to or gain market share.
The large-scale corporate reorganizations and merger movements of the late 1990s, 2006-2008, and 2014-2018 saw a big increase in transportation and warehouse jobs. For now, both are still on the rise (as of March), with employers reporting shortages of workers. That will change as trade collapses.
But the potential disruption by worker actions during a corporate reorganization, as businesses compete for market share, can be a source of leverage, particularly when the economy begins to pull out of the coronavirus crisis and the recession. That can be labor’s “just-in-time” moment of potential power.
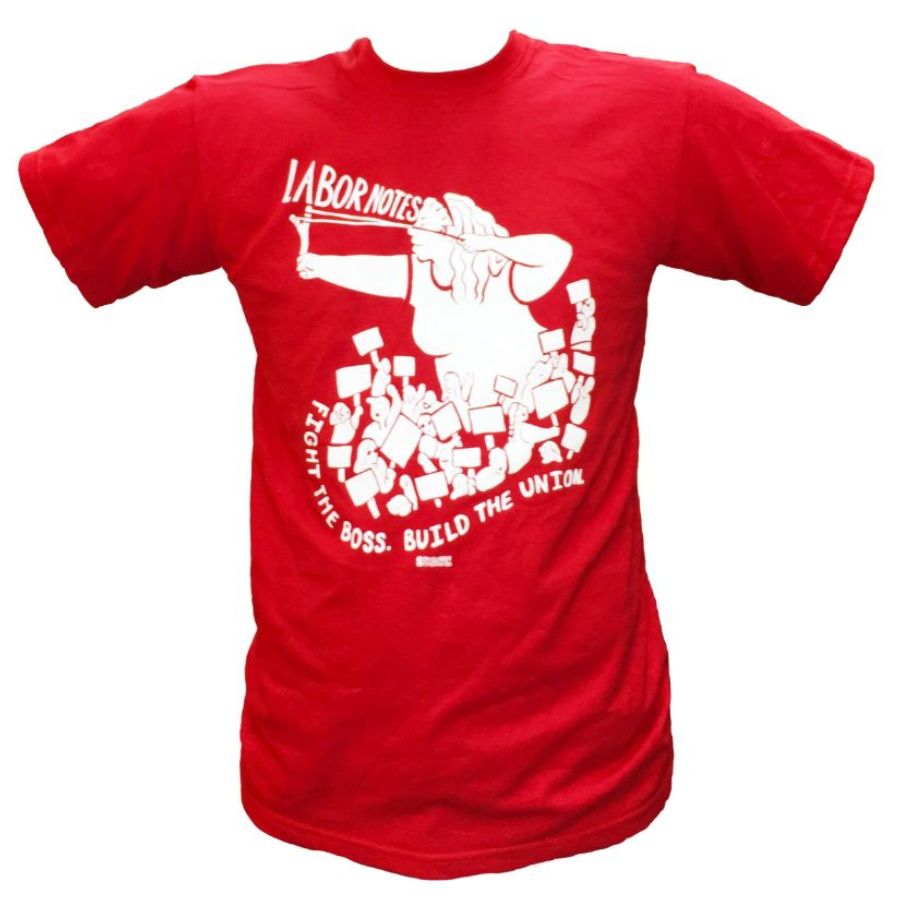
SUPPORT LABOR NOTES
BECOME A MONTHLY DONOR
Give $10 a month or more and get our "Fight the Boss, Build the Union" T-shirt.
In any case, now is the time when workers can intervene to demand all the things they have been denied for decades, including health protection on and off the job. They might not just make demands on employers but confront politicians for universal free health care. The pandemic has made Medicare for All common sense for millions.
This means union support for the actions workers are already taking and encouraging others. It also means building on the awareness millions of workers now have of how essential they are to the system and how little their bosses or the government care about them.
CHANGING UNIONS THEMSELVES
Big growth in organized labor almost always means big changes in the unions themselves and in how employers are forced to deal with them. The rise of industrial unions in the 1930s didn’t happen through orderly Labor Board elections, much less neutrality agreements and card check. It took open-ended strikes, workplace occupations (over 500 sitdown strikes in 1936-37), disruptions in supply chains, community mobilizations, and rank-and-file struggles for union democracy to bring a new labor movement to birth.
In the 1960s and 1970s millions of public sector workers, previously denied union representation by law, also took matters into their own hands. Inspired by the Civil Rights Movement, they took direct action and forced governments to come to terms.
Recently, we have the example of rank-and-file education workers who struck when it was illegal and won the support of working class communities. And now there is the example of workers without union protection, from e-commerce to health care, doing what unions should be doing.
Let’s not squander labor’s just-in-time moment.
Contagion along the Supply Chains
One consequence of just-in-time supply chains was the scarcity in the U.S. of personal protective equipment (PPE); much of its production had been outsourced to Asia by U.S. multinationals like 3M and Honeywell.
MIT logistics guru Yossi Sheffi concluded from the experience with SARS and MERS, “The growing interconnectedness of the global economy makes it increasingly prone to contagion. Contagious events, including medical and financial problems, can spread via human networks that often correlate with supply chain networks.”
Dun and Bradstreet estimates that some 51,000 firms around the world had one or more direct suppliers in Wuhan, while 938 of the Fortune 1000 companies had suppliers in the Wuhan region.
Once the virus had spread, it in turn brought disruption to the centers of production and movement. By the end of February China’s industrial output was down 22 percent and exports off by 17 percent, while 9 percent of world container shipping fleets were inactive.
According to an April UN report, all the places most disrupted as Chinese production fell were also those that were hit early on by the virus. These included the European Union, the U.S., Japan, South Korea, Vietnam, Taiwan, and Singapore—all major trading partners with China.
Kim Moody is a founder of Labor Notes and author of On New Terrain: How Capital Is Reshaping the Battleground of Class War (Haymarket Books, 2017). He lives in London and is a member of the National Union of Journalists.