Six Weeks In, Stock Dwindles at Struck Ohio Battery Plant
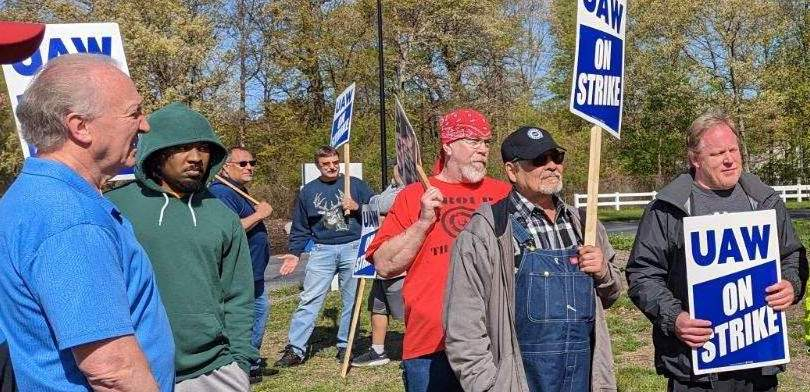
Workers picketed the Clarios battery manufacturing plant in Holland, Ohio. They have been on strike since May 8. Photo: UAW Local 12.
Update, June 14: As we went to press, a third tentative agreement was announced, but without details.
Four hundred auto workers have been on strike at vehicle battery manufacturer Clarios since May 8, rejecting two tentative agreements that fell short of their demands.
“We’re not asking for the moon, we just want it to be a good place to work,” said Andrew Hoertz, a machine operator, citing the company’s decision to cut the piece rates—the incentives workers get paid per battery produced.
The company has pulled out all the stops to prevent any hit to battery production, from stockpiling batteries to weaken workers’ leverage at the negotiating table to shifting production out of this plant, which is near Toledo, Ohio.
The plant pumps out 120,000 to 150,000 low-voltage batteries a week for Ford, General Motors, and retail auto parts sales under brands including DieHard and Duralast.
Clarios boasts that its batteries power 1 in 3 cars in the world. The company is owned by Brookfield Business Partners, part of private equity giant Brookfield Corporation. It has 18 plants in the U.S. and $9 billion in annual revenue.
At the Ohio plant, managers want to cut overtime pay, and workers are having none of it.
The contract expired April 19. Members of Auto Workers (UAW) Local 12 voted down their first tentative agreement in April by 98 percent and then walked out. In May they voted down another tentative agreement recommended by the bargaining committee, this time by 76 percent.
“These contract negotiations have been a tough one,” said Dave Green, director of UAW Region 2B. He said the company has been “more interested in breaking the solidarity of the members than they are in negotiating a contract.”
WRECKING WEEKENDS
Management is proposing to change from overtime pay after eight hours to overtime pay that only kicks in after 40 hours in a week.
The company is also proposing a change in schedule, from eight-hour shifts Monday to Friday, to a “2-2-3” compressed schedule of 12-hour shifts—two days on, two days off, three days on, two days off, etc. Workers say this wrecks weekends and messes with their lives.
Currently workers can volunteer or be scheduled for four hours of overtime, before or after their shift. On off days they can volunteer for four- or eight-hour blocks if overtime is available.
With the proposed changes, there would be no second shift available, so workers would no longer have the option to pick up overtime hours or get time-and-a-half pay on the weekends.
Management says that this schedule change would be limited to new employees and next generation production lines, but workers aren’t buying it. “We’ve seen this before and it wasn’t good for members as a whole,” said Hoertz, referring to tiered working conditions and the division that it creates among workers.
These “alternative work schedules”—dubbed “awful work schedules” by those who work them—are rampant in manufacturing.
MACHINES BREAKING
Workers are also pissed off that their incentive pay rates are being adjusted downwards.
For example, in one department, machine operators are able to get a bonus for batteries made after hitting their production goal. In the last contract, the production goal was protected up until the third year of the five-year contract; after that, the plant manager could increase it.
“I read that in the last contract negotiations, but I guess I thought it would be respected by the company like it’s always been,” said Jeff Monczunski, who has been at the plant for 13 years.
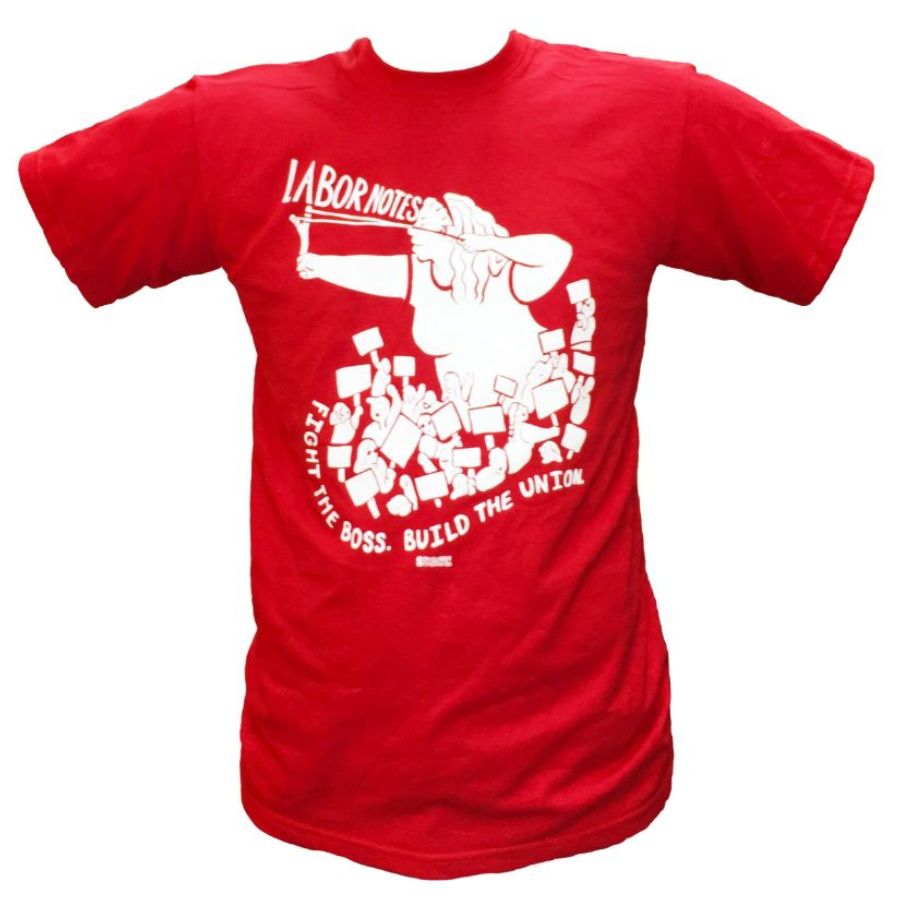
SUPPORT LABOR NOTES
BECOME A MONTHLY DONOR
Give $10 a month or more and get our "Fight the Boss, Build the Union" T-shirt.
No such luck. The production goal that machine operators have to hit in order to receive this incentive pay has gone up twice, so operators have to produce about 25 percent more batteries to make the same pay they used to make. Workers are pushing the machines to their limits just to meet their production goals, let alone exceed them.
“It’s feast or famine. If the machines are running, you can make good money,” said Hoertz. “But now people feel the need to run the machine ragged to make what people used to make. Trying to run the machine nonstop will eventually break the machine down and the whole line will go down.”
DANGER FROM LEAD
On top of pay and scheduling issues, the job is dangerous. They work with lead that has to be maintained at a temperature of 850 degrees—so whatever the temperature is outside, the inside of the plant will be at least 20 degrees hotter, workers said.
Lead is unsafe to consume in any amount; it can be inhaled and ingested, and brought home on clothes. The increased production goals mean less time to clean the machines throughout and in between shifts.
Signs posted all over the plant encourage workers to eat to maintain a full stomach to avoid lead buildup; they have two 15-minute breaks per shift for this reason. However, the break room is far away from their stations, and workers skip eating because there’s just not enough time.
Because of the harsh conditions, workers said, turnover in the plant is through the roof.
“This used to be a really good job,” said Hoertz. “Now when people hear that you have a job here, they wince.”
TURNOVER SOARS
Management has also tightened the attendance policy. Workers are only allowed nine vacation days a year, with no sick days. You get attendance points if you call in sick, and if you rack up 10 points, you’re automatically terminated.
Even managers aren’t staying. Longtime workers said that plant managers used to stay for decades; now they’ve had three in the last eight years.
A week after the strike started, the company got a judge to issue an injunction limiting pickets to five workers at a time at each post.
The company had also imposed a speedup of production in anticipation of the strike. “They’ve been stockpiling batteries for a while, so they have backup to send to plants,” said Hoertz. “But when they run out, the Big 3 won’t be able to make their cars without our batteries.”
Five weeks into the strike, those batteries are running low, workers said. The company has sent letters to all strikers asking them to resign from the union and cross the line. But to the workers’ knowledge, no one has done so. Production is limping along with scabs from temp agencies and managers working on the line.
“They can’t replace all of us,” Hoertz said. “It’s a tough job and it takes a while to learn.”