Skilled Trades Have Different Problem
As in most auto plants, the skilled trades at Toyota have a different set of problems from production workers and therefore different reasons for organizing a union. A blurring line between the two groups of workers also provides some very similar reasons to join.
Here is how some Toyota tradespeople, who prefer not to use their names, describe the situation.
There are seven departments at the Toyota complex: stamping, body shop, paint, powertrain, assembly, plastics, and facilities. The first thing that becomes clear in talking to different tradespeople is that the rules themselves are very "flexible," and vary by department and supervisor.
One tradesman believes that seniority counts for nothing except for picking vacation times.
There is a single maintenance classification. Essentially management can assign you to any work they want. But if you want to transfer jobs, you can apply only if you are "walk-on qualified." Management decides what it means to be qualified.
Management is currently "attritioning out" the skilled workforce. By 2010 they would like to do away with all regular employees not directly involved with putting a part on the car. That includes maintenance workers not involved in directly running the line. No replacements are hired.
OUTSIDE CONTRACTORS
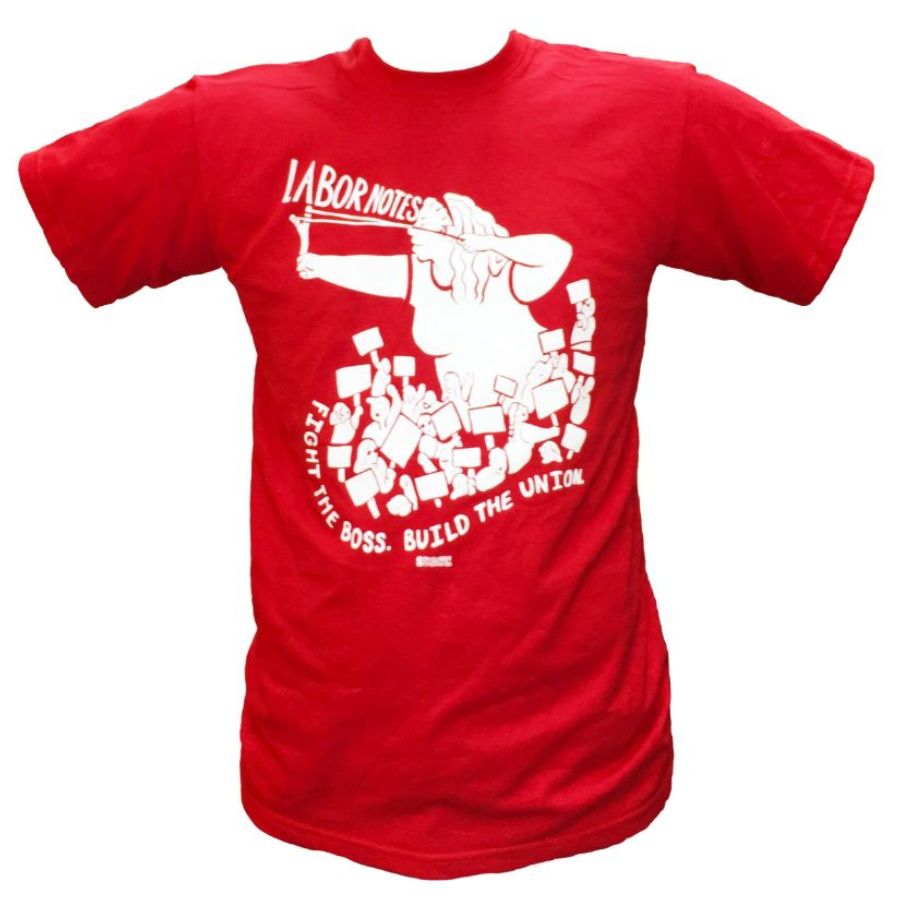
SUPPORT LABOR NOTES
BECOME A MONTHLY DONOR
Give $10 a month or more and get our "Fight the Boss, Build the Union" T-shirt.
"They are looking to move as many of the jobs we do to vendors or outside contractors," stated one worker. "For example, we used to repair equipment and do preventive maintenance on the docks. Now contractors have the work.
"There isn't even much we do in the way of troubleshooting. If there is a problem we are directed to replace a whole module, which is then sent out for repair."
Mostly the downsizing is being done without laying people off. Management takes what it regards as excess people and puts them on special project teams. Management then draws from these teams to replace anyone who leaves.
While this no-layoff policy has attractive features, the other side is management policy that if you are injured you are out. Since the job description of all maintenance workers is to do everything, there is no place for workers who have a medical restriction.
Training for the trades is a three-year program-four hours of classes and four hours of work each day-where workers learn basic hydraulics, machining, and electrical. "But essentially we learn to be machine tenders in specific areas," says a worker. "Few people think they learn enough of any trade to get serious work on the outside."
The line between what skilled and production workers do is blurred. For example, in the body weld section skilled workers change weld tips as do the production workers.
"Since we tend to be machine tenders, some people guard their secrets in the hopes that being needed-the only one who knows-will get them better treatment from management," says one tradesman. "It's just the opposite of the teamwork image of Toyota."