Short Strike Wins for Mitsubishi Workers
Twenty-nine hundred UAW members at Mitsubishi's Bloomington, Illinois assembly plant walked out and won a contract of gains and maintains--a contract we would not have had if our membership had not stood up.
We build the Mitsubishi Eclipse and Galant sedan and the Chrysler Sebring and Dodge Stratus. Back when the plant opened-at that time a joint venture between Chrysler and Mitsubishi--management talked a lot about worker input on the assembly process, being able to stop the line to maintain quality and repair a defect, and QC circles where workers would meet on company time to analyze problems on the job or with quality and come up with alternative methods or tools or parts.
We all learned early on that this was just company ca-ca. Workers' suggestions certainly were not given much consideration and to stop a line was a big no-no. That did not stop the company from bleating that it was real...or the workers from arguing about problems on quality or defects if allowed to pass.
Almost three years ago, a new management team came in and proceeded to reduce or eliminate some of the Japanese work practices that much of the workforce had gotten used to. Over the last two years, the company had experienced record sales and profits, while increasing quality, productivity, and efficiency. In the meantime, the company reduced the amount of manpower via a voluntary buyout while increasing production for those who remained. Those workers who remained had had enough!
In this set of negotiations, the company did not recognize how serious the union membership was until after the contract expired. At 1:30 am on August 24, the UAW walked out. Take-aways were the roadblocks--the company's demands to cut benefits and rules we already had earned and owned and were not about to give up.
JOB ROTATION & ERGONOMICS
When the UAW first organized the plant, the International demanded that each worker only have to perform a single job. The Japanese managers insisted, however, on job rotation because of the flexibility it provided. The union agreed, and as time went along, workers got used to rotating among 5 to 10+ jobs, with a different job roughly every two hours.
Then the American management team that arrived in late 1998/early 1999 decided to attack job rotation as the great Satan against quality. They believed that if workers were restricted to a couple of jobs, they would become experts at those two jobs and quality would go up.
The problem was that full rotation had masked the bad ergonomics of the jobs; limited rotation magnified those same bad ergonomics. Injuries rose.
The union fought the limited rotation to arbitration and lost. Rotation was limited to the same two jobs every day. This is why ergonomics was high on the union's list of demands.
SPONTANEOUS VACATION
The company's demands would have restricted the ability to use "spontaneous vacation" (SPTO) as well as scheduled vacation time. In our contract, 32 hours each year can be taken as "spontaneous" wherein the worker can call in as late as 30 minutes before the start of his shift and tell the boss he is not coming in that day. Half that time can be used in increments of four hours, even to take off the second half of a shift.
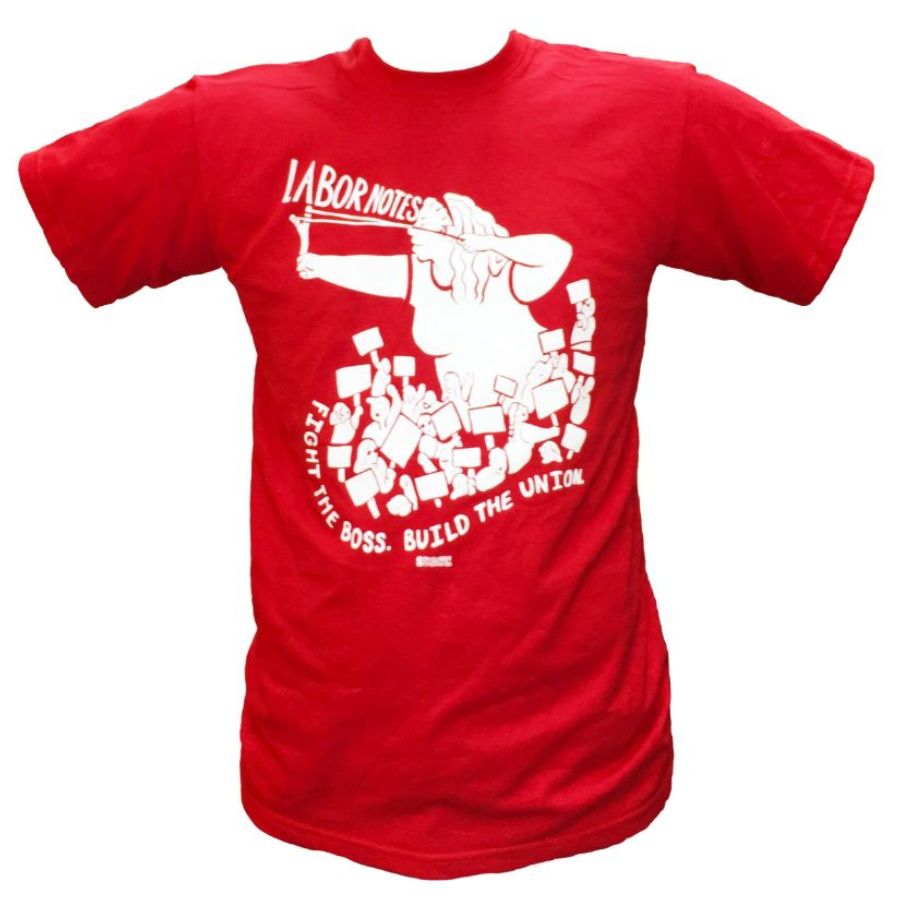
SUPPORT LABOR NOTES
BECOME A MONTHLY DONOR
Give $10 a month or more and get our "Fight the Boss, Build the Union" T-shirt.
Workers have always demanded SPTO because it is their only avenue for dealing with emergencies (car break down, family need) without being disciplined under the company's "no-fault" attendance policy. And workers appreciate being able to deal with a foreman who's over the line simply by going home-or threatening to.
Another Japanese institution, the "Quality-Check" station, was eliminated (and more of that responsibility stolen by the supervisors). Management combined units of workers into larger groups, putting more people under one supervisor and therefore more people under one vacation-day scheduling chart, effectively reducing the ability to schedule time off.
Injuries and job-related stress skyrocketed as working conditions became more hostile. Corporate threats of discipline for work-performance issues only fueled the fire. Outsourced work and seniority rights were also at issue.
WALK-OUT
Within a few hours of our walking out, the company contacted the union to seek a reopening of talks. Meantime, that morning's first shift was arriving. Many second-shift people who had awaited word in the parking lots were there, and they started manning the gates along with the third-shifters who had walked out.
Tremendous solidarity was shown as over a thousand members lined the highway in front of the plant, blocking entrances, slowing traffic, and attracting state and local police (who, other than one particular trooper, were neutral, if not openly supportive).
The scene was something to behold: our first strike, our largest showing of workers banding and bonding together for the betterment of all. The brothers and sisters of our contracted-out cleaning unit walked out in support, as well as the Machinists who grease the machines.
Building trades members refused to cross the picket lines, causing plant expansion work to grind to a halt. Teamster drivers simply parked their transports on the highway, choosing not to pick up any cars for shipment. Unionists from various other locals stopped and offered support.
It was a display of unity across all union labels, one that certainly opened the eyes of the membership as to the true meaning of SOLIDARITY.
Thirty hours later, management agreed to a contract. Now we have a good agreement to work under for the next four years. We gained in wages and benefits, maintaining parity with Chrysler workers, and kept SPTO.
On ergonomics, the UAW and top management will be required to immediately investigate on-the-job injuries and the problem jobs are to be corrected a.s.a.p. The bad jobs in the limited rotations will be given priority attention and all jobs must be re-evaluated every two years.
Justin West is president of UAW Local 2488