Steward’s Corner: Bosses Want to Fix the Worker, Unions Want to Fix the Job
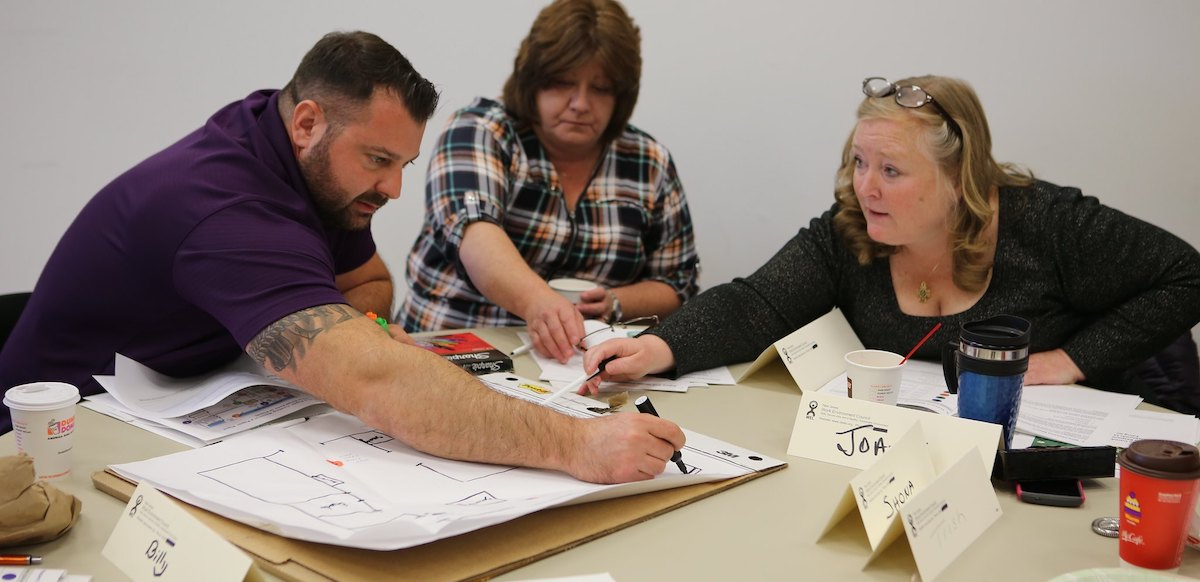
Members of Communications Workers Local 1032 drew a workplace hazard map together at a union safety training in New Jersey. Photo: NJWEC (CC BY-NC-ND 2.0).
Unions and bosses have different outlooks on safety. Employers say illnesses and injuries are caused by worker carelessness: he didn’t look where he was going; she wasn’t using correct lifting technique. That’s the way the boss wants you to think, too.
But the union realizes that it’s the hazards themselves that cause injuries, and that it’s the boss who sets up the workplace, either designing in hazards or failing to design them out. Blind corners and high shelving make it hard to avoid collisions; overloaded boxes on low shelves forces awkward bending. Emphasize these different outlooks with workers.
Bosses want to fix the worker. Their first and often only idea to reduce illnesses and injuries is to require gloves and other personal protective equipment (PPE). They focus on getting workers to work safely by threatening discipline and punishment.
The union wants to fix the job itself. Identify and eliminate hazards. Reduce existing hazards with engineering controls like improving ventilation or safer procedures, slowing down the work, increasing staff, or rearranging the workspace.
The boss wants workers to think about safety his way. But workers become passionate when they start thinking about safety like unions do. Injuries turn from “I did something stupid” to “The boss set me up for this injury.”
Safety can be a way to build connections and power on the shop floor, and can even lead to walk-outs. Workers at the Warren, Michigan, Stamping Plant owned by Stellantis voted May 6 to authorize a strike if multiple safety hazards aren’t fixed.
WORKERS HAVE SOLUTIONS
The boss can’t or won’t figure out how to reduce or get rid of hazards, so we have to show him how. Solution mapping is an easy, participatory activity that finds hazard controls fast. To start, discuss the types of controls below.
Elimination: The best way to control a hazard is to eliminate it. Oily puddles on the floor at Warren Stamping are just one of the hazards workers there face and fixing leaking machines is one of their many demands.
Substitution: Provide less hazardous chemicals to work with. Replace worn-out equipment.
Engineering: These controls protect workers by removing hazards or by using a barrier to keep the hazard away. Examples are machine guarding, providing air conditioning in a hot area, or exhaust ventilation to remove chemical vapors.
Procedures and Training: Use scaffolds instead of ladders. Work on equipment with the power off. Train workers on safer procedures.
Personal Protective Equipment: PPE protects only the user. Gloves and respirators are PPE. PPE is usually the least effective way to protect workers, but if other solutions don’t completely eliminate the hazards, or while they are being installed, PPE may be essential.
Create a Solution Map. Assign each of the above safety control methods a shape or a color. Then workers draw a workplace map and use the shapes and colors to show where each type of control is needed.
It’s amazing how many solutions workers may come up with after the boss says there’s no solution except to change worker behavior. People should keep their maps so they can see how things progress.
WORKERS’ SAFETY COMMITTEE
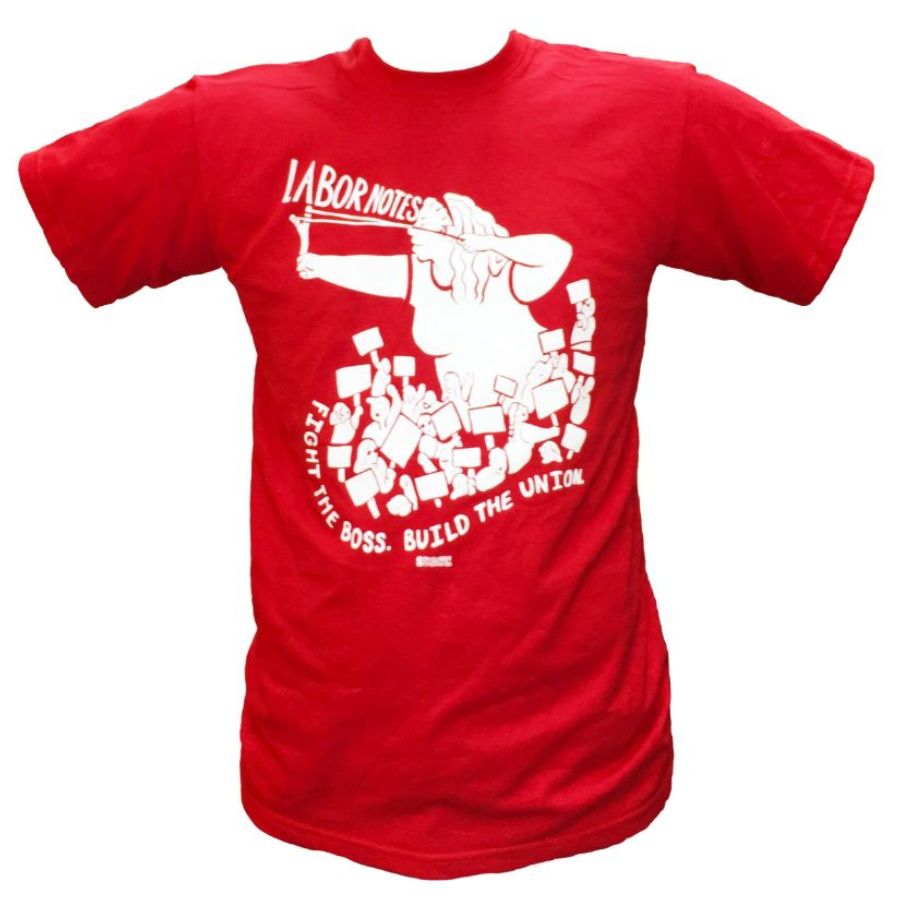
SUPPORT LABOR NOTES
BECOME A MONTHLY DONOR
Give $10 a month or more and get our "Fight the Boss, Build the Union" T-shirt.
This is not the employer’s safety committee. It’s all workers. Hold some open sessions where you start a buzz with training about the union view versus the company view of safety. Then make solution maps.
Choose which issues to work on. Prioritize solutions that affect a lot of people, especially workers who are on the fence about the union. Areas with lots of issues should be high on your list, but pick some easy and quick-to-do solutions too.
Make sure your solutions are specific about what you want. Don’t let the boss implement something that destroys solidarity, like pizza parties for work groups with no recorded injuries.
Make sure you get everyone’s contact info for follow up.
SHOULD YOU CALL OSHA?
OSHA complaints are fine, but they can be slow to get processed. Often, it’s better to just threaten to call OSHA. Employers really don’t like dealing with OSHA. They’ll have to drop everything they’re doing the moment OSHA walks in; it takes up a lot of time and energy. Most employers are at least a little afraid of the outcome. Employers would much rather deal with their employees. They don’t realize how much control you can have.
Bottom line: Don’t expect OSHA to swoop in and solve the hazard in a timely way. But threatening to call OSHA can be a tactic to show that you know your rights and push your boss to take your concerns seriously.
USING SAFETY STRATEGICALLY
Present your list of solutions to the boss. The boss will likely fix some easy stuff. Tell everyone! The union is already helping the workers! Remind workers that the remaining problems are why they are organizing (and if your workplace isn’t yet unionized, why you need a union contract).
Pass around the solution map. Show the workers all the problems the boss won’t fix. Maybe leave a few copies in public places for the boss and customers to see.
Have workers take pictures of workplace hazards. The boss will complain, but banning taking pictures is an unfair labor practice. Publicize the “Hazard of the Week.” Do inspections and publicize the results in the worst areas. Tell your fellow workers and even consider going to the media.
Pass out “At Risk!” stickers for workers to wear where they might be exposed.
Distribute a safety complaint form to be returned to the safety committee. Deliver copies to the boss with deadlines to respond. Make sure everyone knows this is happening. Again, think about going to the media.
Take matters into your own hands. If workers come up with a better procedure, don’t wait for the boss to implement it. Have the workers implement it together.
Workers are always safer in a workplace without hazards instead of just trying to dodge them.
Jay Herzmark is an organizer on workplace safety issues.