Why Organizing Toyota Should Be Job 1 for the United Auto Workers
The future of the labor movement depends on the volunteer organizers at Toyota and workers like them in the growing number of auto plants without a union.
In the long run, union workers cannot keep their wages, benefits, and job security as long as the pace-setters in their industries go unorganized. For now, the Japanese-managed plants offer high wages to keep the union out. But these wages will fall as the unionized auto sector becomes weaker and less of a threat. The unionized companies will follow Toyota in lowering wages. This in turn will force down wages and conditions throughout manufacturing and then in the service sector.
No matter how strong the United Auto Workers might still be at the Big Three, they have little power if the product of the organized plants is not selling in the marketplace. While ultimate responsibility may lie with management-which controls the design, production process, quality, and marketing strategies-the bottom line is that declining sales will have an impact on the strength of the union.
The Asian-owned auto companies account for better than one-third of the U.S. market, including both imports and the cars they build here. They are gaining about two percent per year. It's a large enough number now to significantly influence prices and the market. Greater influence will intensify the already heavy pressure for concessions and further weaken the union.
COMPETITIVE ADVANTAGE
The non-union "transplants" in the industry have a number of critical advantages. Business Week estimates that Toyota has a cost savings of $1,500 per car over General Motors because of the difference in retiree benefits alone.
Partly this is simply the result of a younger workforce. But much is also due to the much greater ability of unionized workers to resist being pushed out before retirement age.
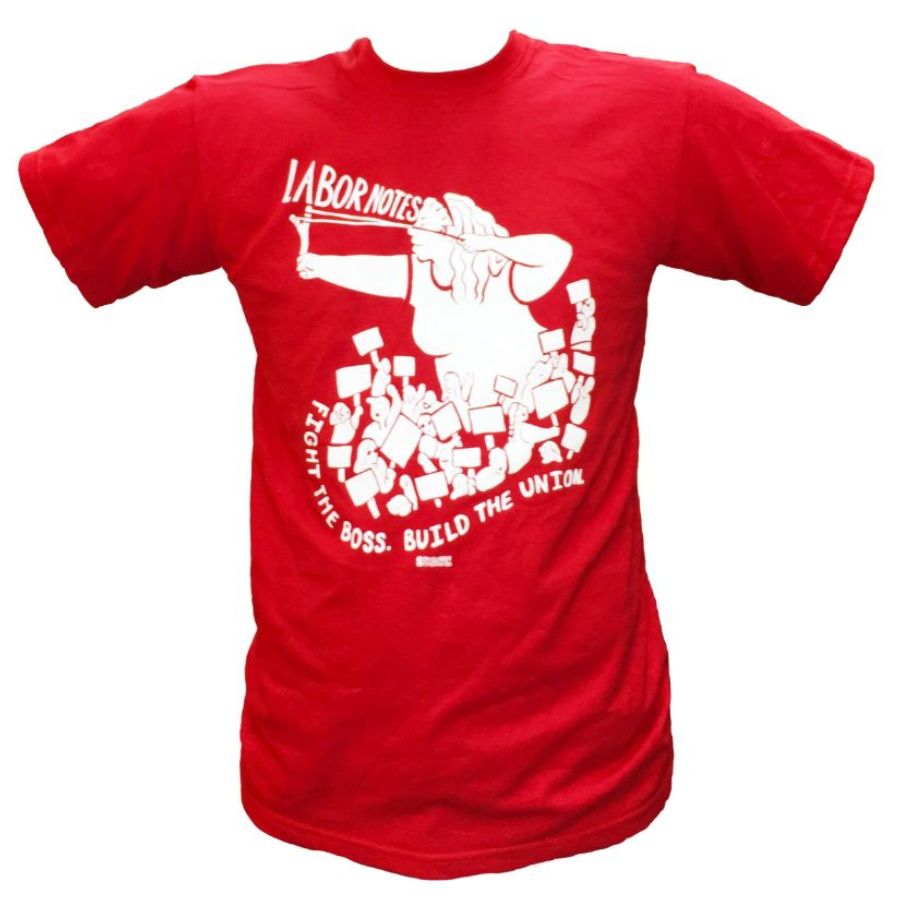
SUPPORT LABOR NOTES
BECOME A MONTHLY DONOR
Give $10 a month or more and get our "Fight the Boss, Build the Union" T-shirt.
Another factor is the benefits themselves. The defined-benefit plans in the UAW plants provide more security but cost the companies significantly more.
Toyota achieves further savings through freedom from the union's work rules, outsourcing restrictions, and safety programs. Without a union to stand up for human dignity there are few restraints on Toyota's continuous squeezing of the workforce.
Unionized workers typically do cost their companies more. The whole point of unions is to force management to consider workers' needs, even if they hurt the bottom line.
THE TOYOTA MODEL
The pressure to reduce the workforce, benefits, and working conditions is not only a product of market competition, however. The Toyota production system is the model for U.S. management. Toyota is the benchmark. Recent articles from the Harvard Business Review, "Learning to Lead at Toyota" and "DNA of the Toyota Production System," are required reading for Chrysler management.
The auto industry is an excellent example of the brutal truth "organize or die." It is also a demonstration that it is not enough simply to organize for numbers. The labor movement must organize the leading corporations in each sector or lose the sector.
It isn't enough for us to doff our union caps to the courage of the Georgetown volunteers. It is in our most immediate interest to do everything we can-to use all the resources of our union-to make sure that they succeed.