A Union Is Brewing at Virginia Lipton Factory
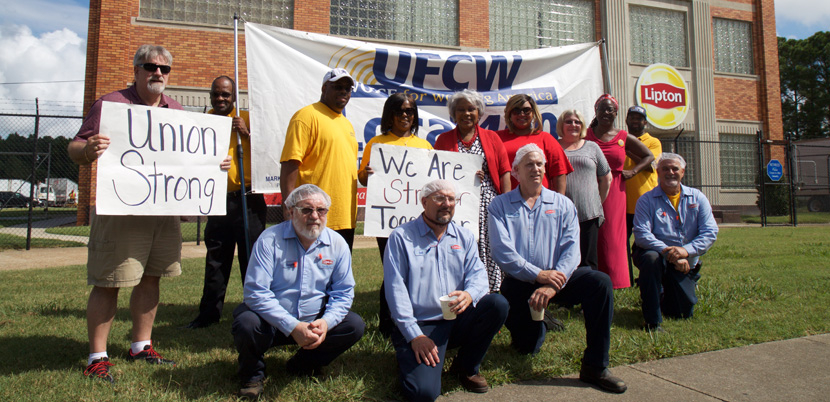
Lipton tea factory workers are now members of Food and Commercial Workers (UFCW) Local 400, after workers voted 108-79 to join the union. Photo: UFCW Local 400
What pushed tea factory workers to their boiling point?
In August the workers who supply Lipton’s entire North American market voted 108-79 to join Food and Commercial Workers (UFCW) Local 400.
They were fed up with an unrelenting schedule that produces constant fatigue, injuries, and broken relationships.
Lipton brings tea from around the world through the Port of Virginia. At its single 20-acre plant in nearby Suffolk, 200 workers roast, blend, package, and warehouse it, producing over 6 billion bags a year.
For years on end, these workers have been “drafted”—the company’s term for forced overtime—into working 13 straight days out of every 14.
When workers quit or took leave, Lipton refused to replace them. The more overtime the company demanded, the fewer workers remained… and the fewer workers remained, the more overtime the company demanded.
“That was the nail in the coffin for the majority of us,” said Robert Davis, a mechanic who works on machines in the plant. “They threw it on us with no remorse.”
The grueling schedule is one hallmark of the brutal methodology that’s used to manage this factory: lean production.
First developed in auto manufacturing, lean management has long since infiltrated such industries as logistics, health care, hotel work, and education. Lipton’s job postings for supervisors are peppered with such lean buzzwords as Total Production Manufacturing, Six Sigma, and “continuous improvement.”
From a worker’s point of view, the method is better understood as management by stress. Workers are subjected to competitive pressures—including repetitive stress, speed-up, and job insecurity—that force out those who can’t handle the pace, and squeeze ever more productivity out of those who stay.
INVESTING IN MACHINES
Until recently, a quarter of the Lipton workforce was made up of temporary workers hired by the multinational agency Manpower. Their jobs ranged from heavy lifting in the warehouse to packing cases full of tea on the production line.
Most of the temps made around $8 an hour, a fraction of what full-time Lipton employees got. They were allowed to work a maximum of 1,000 hours or six months before being discharged.
Issues in the plant started to simmer in 2013, after Lipton’s parent company Unilever announced it would invest $96 million to upgrade the factory.
Production shut down while the new equipment was installed. And regardless of how long they’d been with the company, the Lipton workers were all forced to apply for their own jobs.
“I had been there 23 years, but I had to reapply for the same job, turn in a resume and everything,” Davis said.
His first application was turned down. “The second time around, I finally made it,” he said, “to keep doing the same job I have been doing for over 20 years.”
Workers got the message: we’re investing in machines, not in you.
SKELETON CREW
It was after the new machines were installed that Lipton started demanding more and more overtime from its shrinking base of full-time employees.
“We needed to hire,” said Philip Surace, who’s been a Lipton mechanic for 15 years. “Instead, the company started drafting people. For years now, it’s been a skeleton crew running the plant.”
The factory runs 24 hours a day. Shifts are 12 hours long—day or night, depending on seniority.
“It was unsafe, but the company will never admit it was unsafe,” Surace said. “People went out on FMLA [unpaid medical leave] because their bodies wouldn’t hold up.”
Management abolished sick days—even unpaid ones, apart from the legally mandated FMLA—and instituted a stringent system of attendance points.
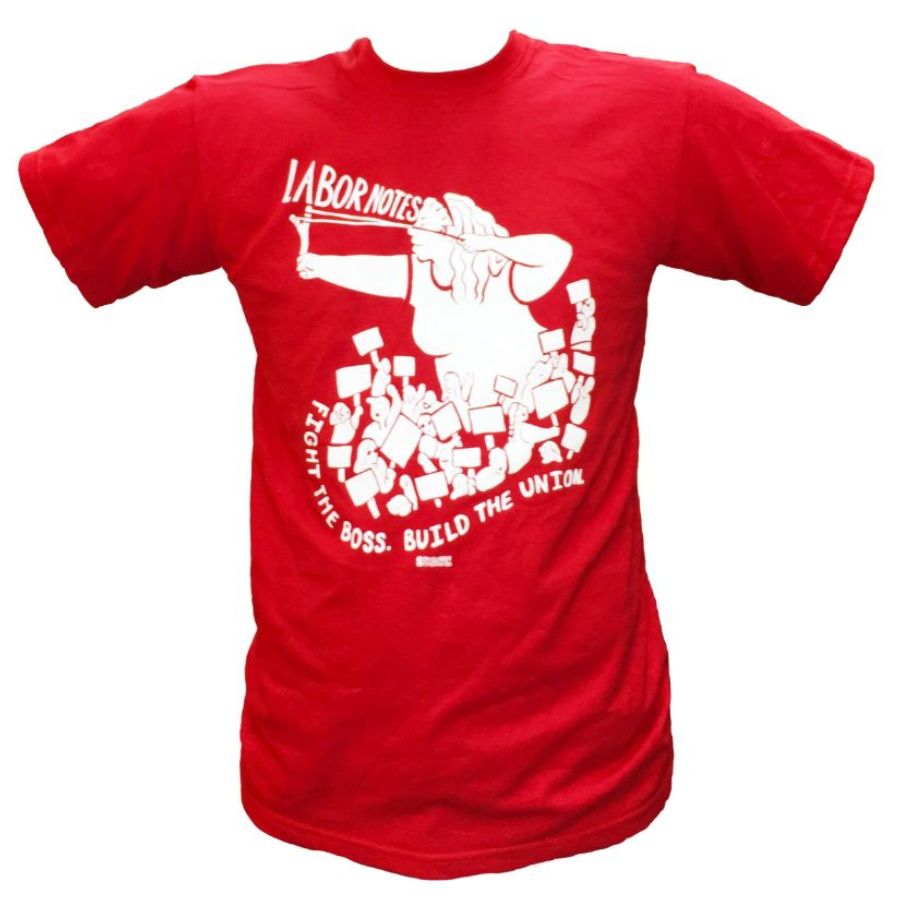
SUPPORT LABOR NOTES
BECOME A MONTHLY DONOR
Give $10 a month or more and get our "Fight the Boss, Build the Union" T-shirt.
If you missed work, arrived late, or left early, regardless of the reason, you would receive an “incident” in your file. Eight incidents in any one-year period meant you were automatically fired.
Even when sick or injured, many workers were afraid they’d lose their jobs if they missed work. Pay at the plant is high for the region. Hourly wages start at $21, and most workers make $26-$27.
“You had a choice to make,” said Anita Anderson, a trainer and line worker who’s been with the company 10 years. “You call out sick and get one incident, or you come to work and pass germs around.”
The incident system also discouraged reporting injuries. Like many employers, Lipton takes a blame-the-worker attitude to workplace safety.
“If you got hurt on the job, it’s never unsafe conditions,” Anderson said. “It was never that you were fatigued from working so many hours. It was always, the employee did not do something right. So if you get hurt, then it’s an incident, it’s a strike in your personnel file.”
TALKING IT UP
After years of steeping in the relentless work schedule, dangerous conditions, and lack of sick days, the Lipton workers were ready to organize. UFCW Organizer Kayla Mock could see that they were serious when their first meeting drew 32 people.
“From the beginning, they took so much ownership and responsibility for building their union,” Mock said. “They held full-on organizing conversations with their co-workers, identifying other leaders in the plant and bringing them on board, talking and assessing the other workers.”
Soon Lipton workers were meeting regularly with UFCW staff to review lists of employees, debrief their organizing conversations, and share their assessments of how each co-worker would vote.
Many people were unfamiliar with unions, said Corey Hicks, who troubleshoots and repairs machines in the plant. So he talked about how a union could address the issues they cared about, like the schedule and the rising cost of insurance.
“Right now, the company just gives you what they want to give you,” he would explain to co-workers.
“It’s a dictatorship. With a union you can bargain all of these things.”
Unilever owns one other union factory in the U.S., a Hellman’s Mayonnaise plant in Chicago. The UFCW organized a conference call where Lipton and Hellman’s workers compared notes.
“We decided we deserved more than what we were getting,” Anderson said. “Once we got a write-up comparing the benefits of the Hellman plant compared to our plant, a lot more folks came on board.”
Since she had recently transitioned from night shift to day, Anderson often stayed after work to talk to people she knew. Some co-workers were afraid the plant might close if they voted union.
“I told them about how the Verizon workers had a union,” she said, “and when they were threatened with their jobs going overseas, they went on strike, they fought, and they won and kept their jobs.”
VICTORY IS SWEET
Reading the tea leaves, the company let go all the Manpower temps and started backing off the mandatory overtime. “Once the word ‘union’ was mentioned, suddenly they started to hire people,” Surace said.
“What they told us for years was that they couldn’t find quality people who could pass the test the company gives to potential hires. What did they do, put something in the water to suddenly make people smart?”
The plant manager also held a mandatory anti-union meeting and sent out a letter discouraging unionization.
But luckily for the workers, global activists already had Unilever on the defensive. Under pressure after poisoning factory workers in India with mercury and exposing tea plantation workers in Kenya to sexual harassment, the corporation has been trying to rebuild its public image by touting a newfound commitment to human rights.
So when UFCW representatives brought up Lipton’s union-busting tactics, Unilever was disposed to head off another headache. It immediately replaced the plant manager and the head of Human Resources.
Throwing out the boss helped bolster workers’ confidence in the union.
Next on the agenda is negotiating a first contract. “Everyone is excited,” Anderson said. “Even the ones that were naysayers about the union are asking about the next union meeting so they can speak up and talk about the issues in the plant.”