Auto Workers Use ‘Just-in-Time’ Leverage To Organize Parts Plants
Workers at DaimlerChrysler’s Toledo, Ohio Jeep plant found themselves out of instrument panels to install-and on the street-for two days in June. The United Auto Workers had called a strike at the company that sends instrument panels to Jeep-Johnson Controls in Northwood, Ohio-to press the company to recognize the union.
At the same time, the UAW struck three other Johnson Controls plants in Oklahoma City; Earth City, Missouri; and Shreveport, Louisiana, to press for a first contract at those plants. The strikes involved 700 workers and slowed down or halted production at five final assembly plants-three DaimlerChrysler and two GM- dependent on Johnson Controls for seats and other parts. Two of these plants produce the popular SUVs Chevy Blazer and Jeep Liberty.
The UAW struck after over a year of fruitless contract negotiations and a nasty anti-union campaign-and during new UAW President Ron Gettelfinger’s first week in office.
The strike was planned by Gettelfinger and Vice President for Organizing Bob King. King has now been placed in charge of the union’s parts workers division as well as the organizing department.
TWO-DAY STRIKE NETS BIG GAINS
Two days of non-stop negotiations ended the strike on June 14 and produced big gains for the union, with three first contracts including $1,500 signing bonuses, wage hikes of $3 or more, a new pension plan, tuition assistance, seniority and grievance procedure rights, and plant closure prohibition.
HITTING "JUST IN TIME"
Johnson Controls also agreed to “card check neutrality” for Northwood and 26 of its other plants, opening the door to organizing 8,000 workers in the overwhelmingly non-union auto parts industry. This means the company will remain neutral in the UAW’s organizing drives and will recognize the union where a majority of workers sign cards, without an election.
George Windau, who works at Jeep in Toledo, said the strike was “so devastating on production simply because of the ‘just in time’ supply philosophy used in the plants, which relies on a steady and continuous flow of these parts from Johnson Controls.”
Targeting “just in time” production was also an important tool during strikes at Johnson Controls plants in Oberlin, Ohio and Plymouth, Michigan in 1997. Workers walked out to stop the flow of seats and other parts to Ford assembly plants, which produced models such as the popular Ford Expedition.
When Johnson Controls said it would bring in replacement workers, the union threatened to move the picket line to Ford if the company accepted scab parts. In an unprecedented move, Ford management told Johnson Controls it wouldn’t accept parts until the labor dispute was resolved.
Though using the leverage of “just in time” production against the Big Three showed the strength of the union, it is likely that this strike’s fate, like the one in 1997, was largely predetermined behind the closed doors of UAW and Big Three boardrooms. The strike’s quick resolution suggests that GM and DaimlerChrysler played a considerable role in negotiations from an early stage.
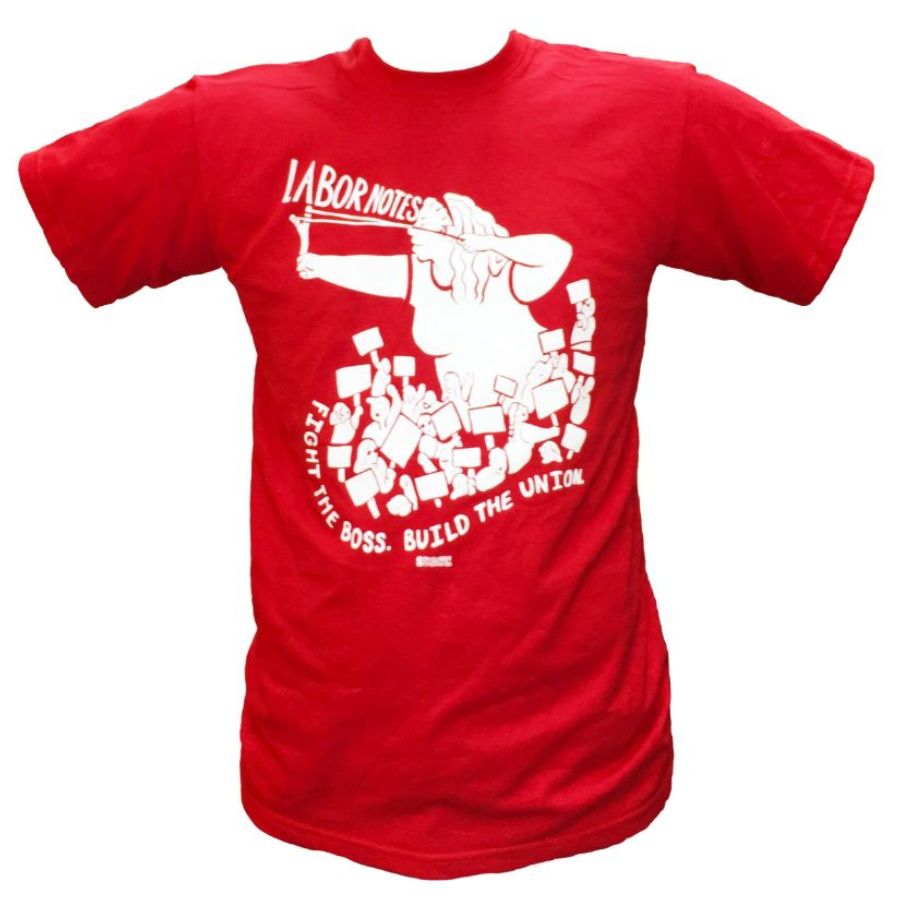
SUPPORT LABOR NOTES
BECOME A MONTHLY DONOR
Give $10 a month or more and get our "Fight the Boss, Build the Union" T-shirt.
In 1997, Ford was quick to point to its relationship with the union when it announced it would not take scab parts from Johnson Controls. This time, GM and DaimlerChrysler said that they were “close” during negotiations, but would not elaborate on their roles.
The cooperative relationship between the union and the Big Three could be tested when bargaining over new contracts begins next summer.
FINALLY ORGANIZING
Johnson Controls, like the rest of the auto parts industry, is only partially organized. Over half of parts production workers were organized in the 1970s, but the union’s share has slid to below 20 percent today. The UAW watched as the Big Three closed or spun off many of their own parts plants, aiming, eventually, to reduce labor costs.
These plants are still unionized and pay well, but the non-union, lower-wage suppliers such as Johnson Controls gained Big Three contracts by undercutting costs-and took a larger share of the industry. The UAW appeared to have no strategy for organizing the non-union plants.
From 1980 to 1992 the union spent well under 5 percent of its annual budget on all organizing initiatives and focused on picking up independent unions or on sectors other than the auto industry. Lack of organizing is reflected in overall membership numbers, which have dwindled steadily from over 1.5 million members in 1979 to 671,953 in 2000.
In 2001, the union saw its first growth in decades, bringing membership up to 701,818. This 4.5 percent increase came largely from non-auto sectors.
Gettelfinger declared at the UAW’s convention in June that organizing the parts sector is a necessity. His success at Johnson Controls stands in contrast to his dealings with a strike by Local 2036 at another parts supplier, Kentucky-based Accuride.
As then-Region 3 Director, Gettelfinger authorized the Accuride strike with strong words of encouragement: “Go get ‘em!” Strikers soon realized that the union was offering a pep talk without a strategy to win. UAW higher-ups say they asked Accuride’s final assembly customers to intervene, but got no results. Throughout, scab parts made at Accuride fed the plants.
At Johnson Controls, the union’s card check neutrality agreement could lead to near-complete unionization of that central parts supplier within the year. Gettelfinger and Bob King, vice president for organizing, may use the same strategy at the other big auto parts players, including Dana, Magna International, and TRW.
Joanna Dubinsky is a member of UAW Local 2322, the Graduate Employee Organization at the University of Massachusetts-Amherst. She’d be glad to see her union prioritize organizing the auto parts industry.